Long after its contents have been unpacked and used, the humble cardboard box can keep on working. Finding a second life for a box is relatively simple in the home, where it can help organize storage in a basement or closet, serve as a play hideout for kids and even morph into an end table. Boxes can also find new uses on a commercial scale. “Everyone sees a box every day of their lives,” says Mary Linn Leonards, chief financial officer of American Box & Recycling, which helps connect businesses that need boxes with those facing mountains of cardboard. “Off-brand retailers can reuse the boxes to pack material that goes to stores; they’re not customer facing,” Leonards explains.
American Box & Recycling began in 1956 when the founder, Stuart Parmet, in his work with Tastykake, encountered one customer swamped with too many cardboard boxes and then another saying he needed them. Parmet devised a matchmaking operation, and now, three generations later, the company has diverted more than 1 million tons of cardboard from landfills.
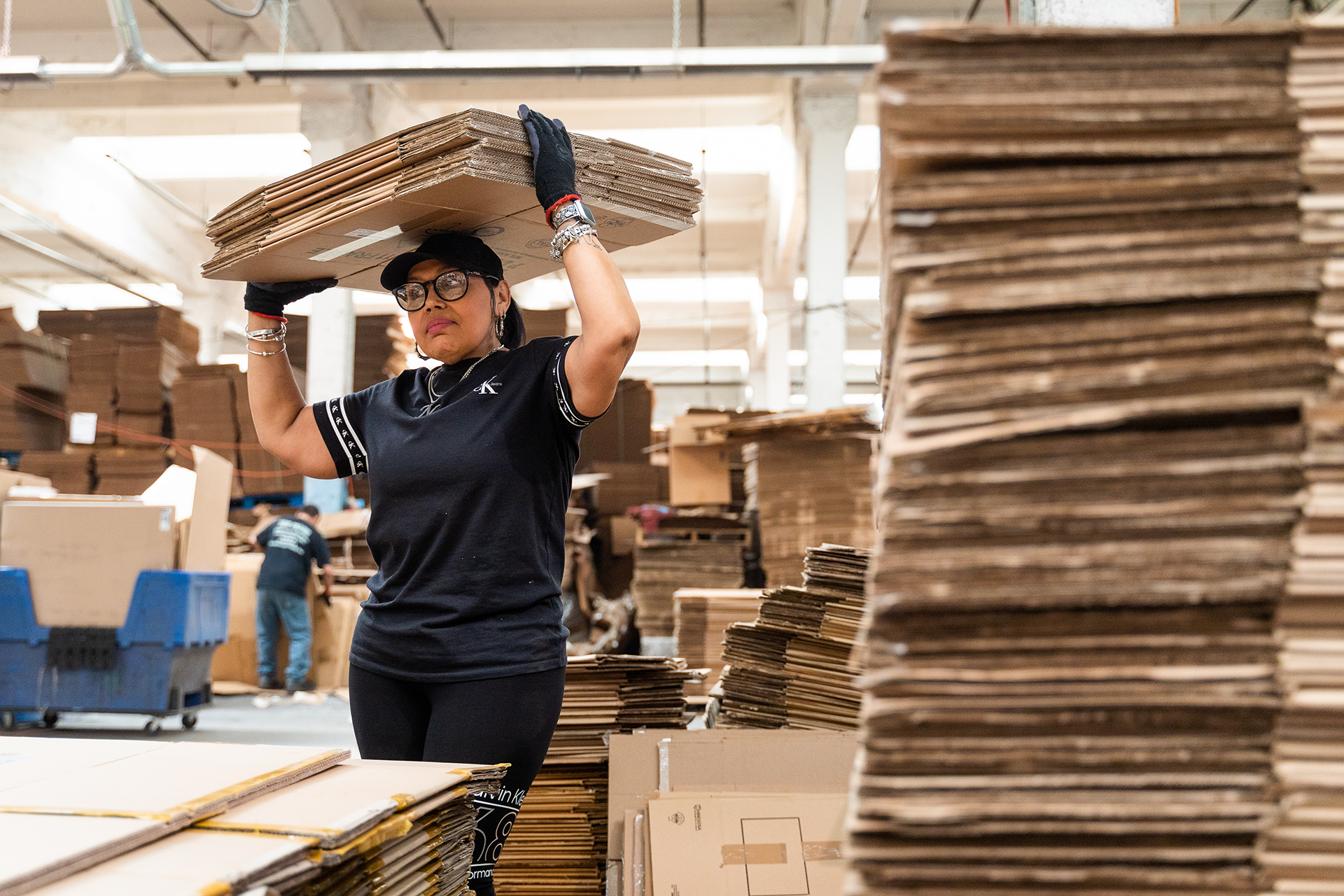
Reusing boxes doesn’t just save cardboard. According to a peer-reviewed study on the lifecycle of corrugated cardboard boxes published in Resources, reusing a cardboard box once instead of recycling right away cuts its lifecycle emissions by a third.
Over the years American Box & Recycling has saved 4 million trees, 100 million gallons of water and 50 million pounds of carbon emissions, according to the company website. “We were a landfill diversion company,” Leonards says. “But that’s just the beginning — to go from landfill free to zero waste.”
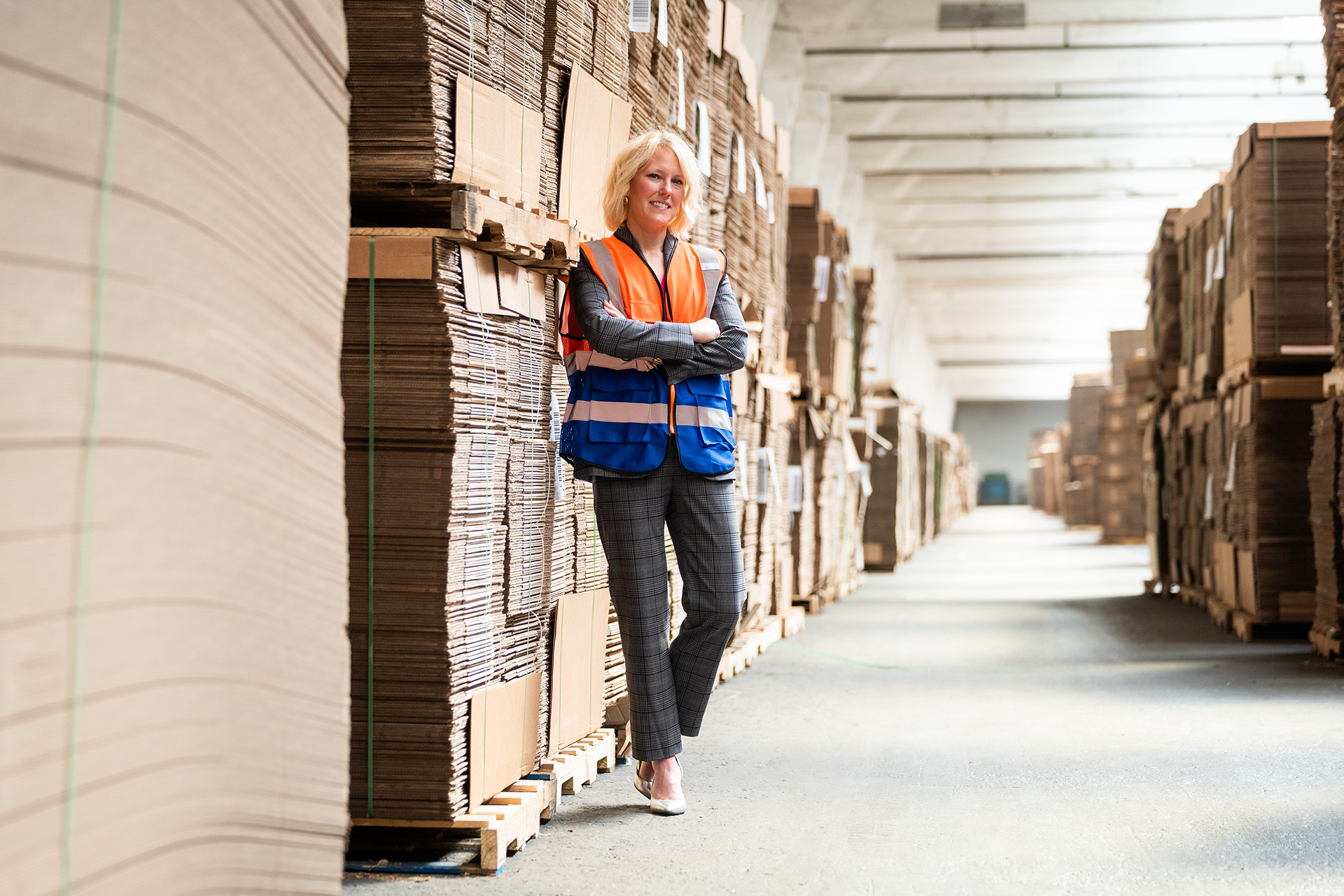
A new division, IMPACT Recycling Partners, offers sustainability auditing for total resource use and efficiency (TRUE) through a program, Green Business Certification, Inc. (GBCI), initiated by the U.S. Green Building Council. According to Steven Dege, a TRUE advisor and director of business development and sustainability programs at IMPACT, the process demands companies continuously evaluate their waste stream and look for solutions through composting or reusing materials to put them into a circular system.
Achieving true zero waste, defined as diverting 90% of waste from landfills and incineration, is a two-level process that takes 12 to 18 months and is overseen by a GBCI auditor. Pre-certification in the first six months sets companies up for full certification six months later. “The waste data must be collected every month of every year to monitor it,” Dege says. If the data shows an increase in waste, Dege must analyze why.
American Box & Recycling operates from Philadelphia to Pittsburgh and beyond, through Ohio, Wisconsin and North Carolina. IMPACT is just getting started with one client in Philadelphia and two based outside of the city.
Dege begins the trainings before handing the instruction over to the clients’ supervisors. “We develop the necessary training tools and let them take over,” he says. “It empowers them; they’re good at it. Employees are buying into it.”
“The number one problem we have is wrong habits,” Dege says. This is as true at the workplace as it is at home. “If everyone just washed out containers for recycling and set up a small composter for food waste, it would go a long way.”
There’s always a solution. Sometimes there’s a cost behind it. You have to be willing to pay that cost.”
— Steven Dege, Director of Sustainabiltiy Programs, IMPACT
Through fostering good habits and analyzing what gets thrown away, it is possible to get to zero waste. “We should be able to handle all of the waste,” Dege says. For clients “we’re transparent about letting them know what kind of products the materials go into,” he says. “There’s always a solution. Sometimes there’s a cost behind it. You have to be willing to pay that cost.”
Going zero waste can save money. Insurance is one area of saving, Leonards says. “Their insurance decreases because there’s less risk. In this process, everything can be traced throughout its lifetime, but if it goes into a landfill, there’s no traceability. So one doesn’t know what will happen to that material, which means there’s increased risk.”
Leonards, who got her start in industry by driving a 53-foot truck to pick up hazardous waste, says she’s passionate about the work. “Zero waste is what we do. We look at an entire company from the front door to the back door. We’re picking apart the process from start to finish so that nothing goes out the back door to the landfill.”